これまで「切削と研削の違い」「砥石」について説明しました。分からない場合は過去記事を参照してくださいね。具体的な加工手順やいろいろな研削盤の構造を理解しないとメリット、デメリットや出来ること、出来ないことを理解できないです。この研削加工を学ぶのに最もポピュラーでわかり易いのは平面研削盤です。今回は平面研削盤を説明することで、研削加工の取っ掛かりが理解できればと思います。
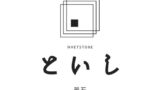
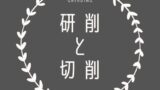
1.構造
図を見れば、一目瞭然なんですけど、、、主に平面研削盤とは以下のような構造です。
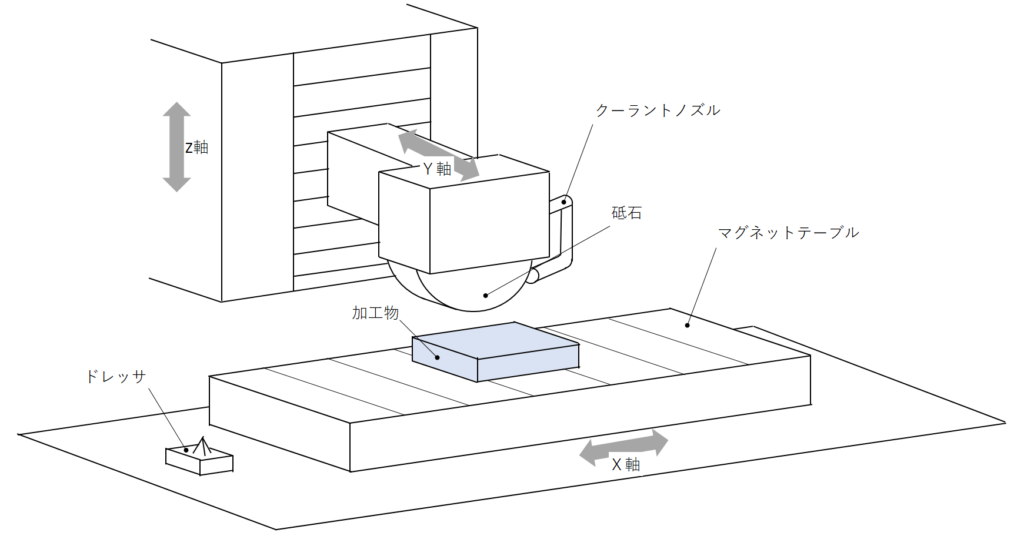
稼働軸はXYZの3軸で、X軸はマグネットテーブルのストローク、Y軸は砥石軸の手前奥側へのストローク、Z軸は砥石軸の上下の位置決めで主に砥石の切り込み量を調整します。
テーブルマグネットは電磁式で着磁、脱磁のon/offを行い、加工物のチャッキング(固定)を行います。
なお、研削盤には小型のクーラントタンクが設置され、フィルタでスラッジ(加工した研削屑)を除去したものがクーラントノズルからは排出されます。
ドレッサは砥石の成形を行う為に使用され、マグネットテーブルの下に設置されることがあるが、ドレッサーは台座ごと取り外し、加工物の形状に応じてさまざまな場所に移動させることもできます。
2.砥石
研削盤で加工するにはまず砥石を準備しなければなりません。砥石を準備してから加工ができる状態までは以下のようなステップがあります。安全対策として必ず知らなければならない項目もあるので読み飛ばさないように!
2.1 クラック確認
砥石は砥粒と呼ばれる石の粒を焼き固めたもので、お椀や皿と同じで陶器のように衝撃に弱く簡単に割れてしまいます。砥石が完全に割れているのであれば良いのですが、目に見えないようなひび(クラック)があると加工中の負荷により、砥石が砕けて重大な人身事故にもなりかねません。そのため使用する砥石をハンマの柄(木製)で軽く叩き、甲高い音がすれば正常な砥石で、鈍い音がすると砥石にひびがある可能性があるため誰がなんと言おうと、危険なのでその砥石の使用はいますぐにやめましょう。
2.2 フランジ取付け
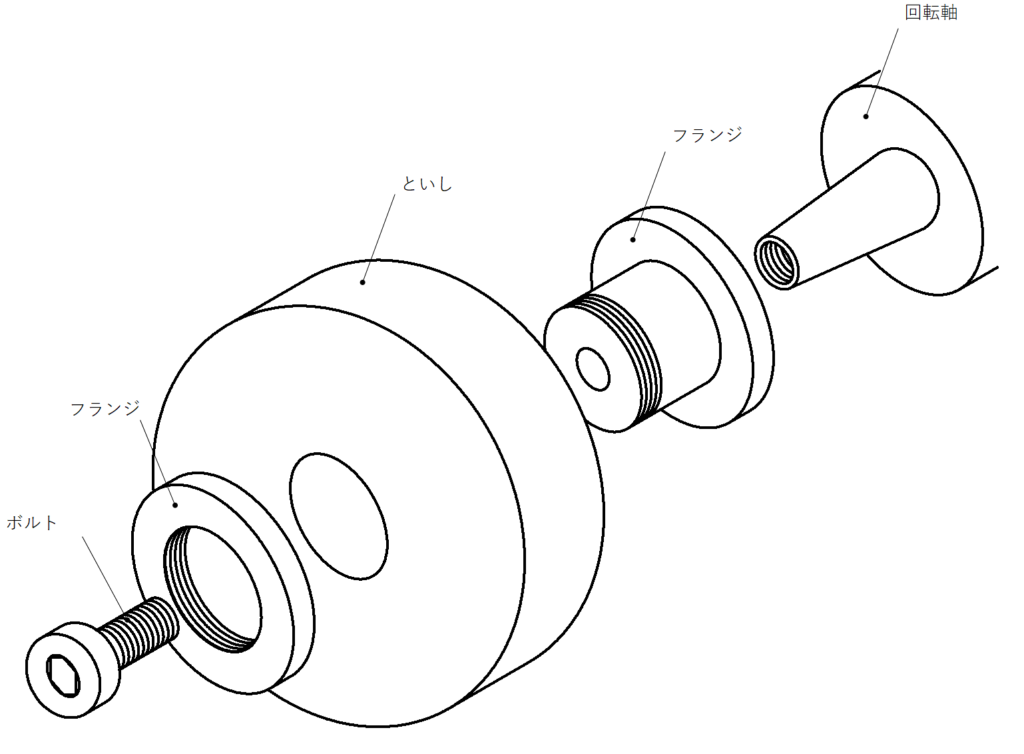
砥石はフランジと呼ばれる円盤状のもので砥石を挟み込み、フランジごとスピンドル軸にボルトで固定しています。砥石は周速度1000~2000m/secで回転するため、フランジはハンマーで叩き、きつく固定しましょう。このフランジの固定が十分であるかを確認するために取り付けた砥石を一旦、高速回転させ、即座にストップし、砥石とフランジにゆるみが生じていないかをチェックします。なお、フランジを固定するボルトは自動車のタイヤと同じで砥石の回転方向とは逆にしめつけますので、多くの場合は左ねじです。
2.3 バランス確認
交換した新品の砥石は回転軸に対して重心のバランスが悪いため、砥石のバランス取りをする必要があります。そのためフランジにはバランスピースと呼ばれる稼働式のおもりが3つあり、その3つのおもりの間隔を調整することで砥石の重心バランスを正常にします。このバランスが悪いと回転軸が振動し、研削加工面にビビりが生じたり、最悪は砥石がゆるみフランジから外れることも懸念されます。また砥石のバランスが正常であるかを確認するのにバランサーと呼ばれる振動計があるので、その計測値を利用してバランスピースの位置を微調整して砥石のバランスを取ります。
2.4 ツルーイング
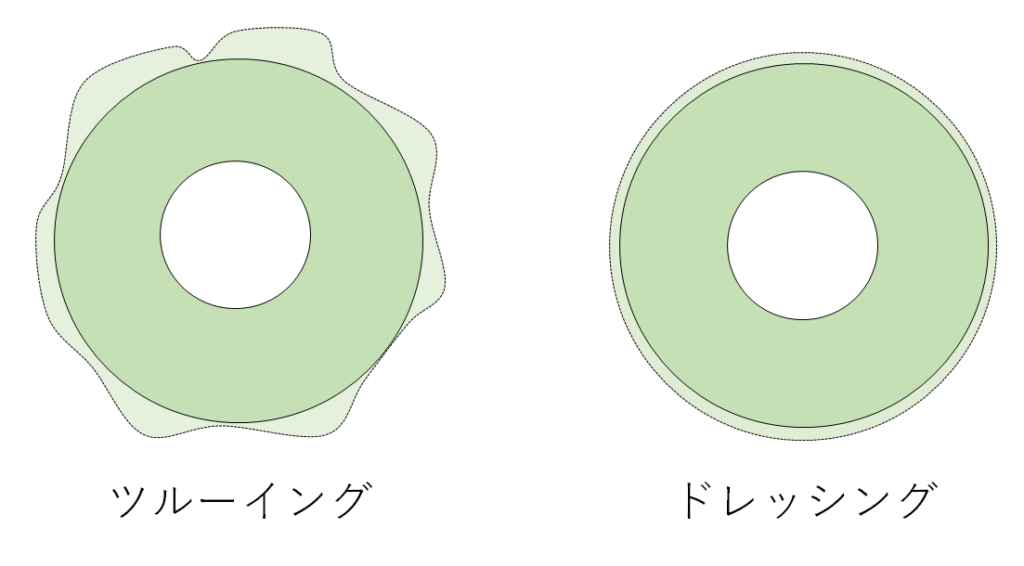
新品の砥石外径は真円でなく、回転軸に対しても同軸ではありませんので、砥石外径を削り落とします。これをツルーイングと呼びます。ツルーイングはドレッシングと混同されがちですが、ツルーイングは砥石外径を加工すべき形状に砥石を成型することを指し、ドレッシングは砥石の切れ味を確保するために砥石を一皮めくるようなイメージです。
ツルーリングは砥石全周がドレッサーにより削り落とされていなければならないため、砥石外径をマジックで着色し、ツルーリング後に着色した部分が残存していないことを確認します。
3 加工液の種類と目的
加工液には「工具(砥石)と加工物との摩擦抵抗を小さくするための潤滑」「摩擦熱を押さえる冷却」「加工によるスラッジ、切り粉などを排出するための洗浄」としての役割があります。また加工液には以下の大きく3種類の加工液があり、それぞれの用途に合わせて使い分けをします。
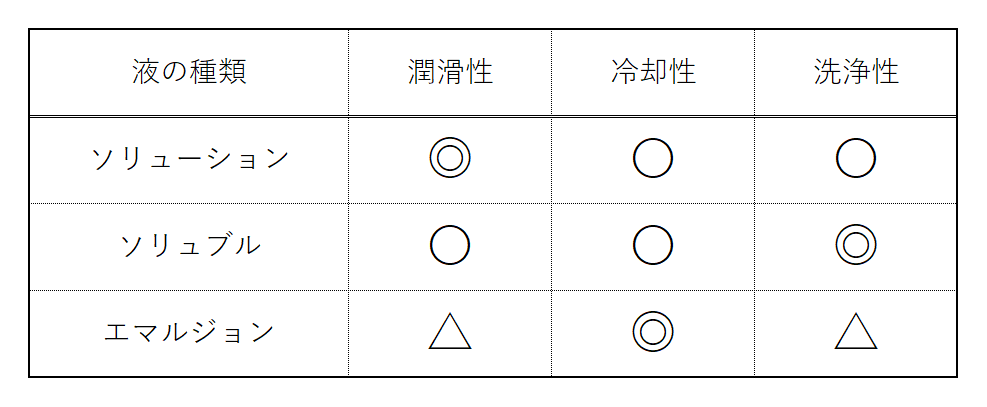
ソリューション:
鉱物油が0%で100%水溶性の研削液。冷却性に優れているため研削加工に用いる。
ソリュブル :
鉱物油が5~20%を含んだ水溶性の研削液。
エマルジョン :
鉱物油が50~80%の液。潤滑性能が高いため研削ではなく切削加工に向いている。
研削液のほとんどは原液を水で希釈するタイプで、希釈割合は使用用途によって変わります。濃度が高い場合はノズルやポンプ内で詰まったり、洗浄性が低下することはありますが、極端に高濃度でなければ大きな問題は生じません。しかし、濃度が低い場合は潤滑および冷却性能が低下し研削焼けやびびりなどが発生する可能性が高まります。また研削液は時間と共に水位が低下するため、液を追加する度に濃度管理をする必要があります。濃度管理は市販されている濃度計を使用して管理すれば、問題ありません。
研削液はポンプを使用して、液層からクーラントノズルへ研削液を送り、排出されます。多くの場合、液層には液面高さを確認するゲージがついており、定期的に液面高さを管理することができます。研削液には多くのスラッジ(切り粉)が含まれている為、フィルタを通過してから液層に送り込まれますが、それでもスラッジのすべてを取り除くことはできませんので液層の上澄みだけをポンプからすくい上げてからクーラントノズルへ送られます。そのためポンプは液の高い位置に設置されているため、液層内の研削液が少ないと液をすくい上げることができないばかりか、ポンプが空運転を続けると破損する恐れもあるため、液面管理は定期的に行う必要があるのです。
4.マグネットテーブルのセルフ研削(ベット研磨)
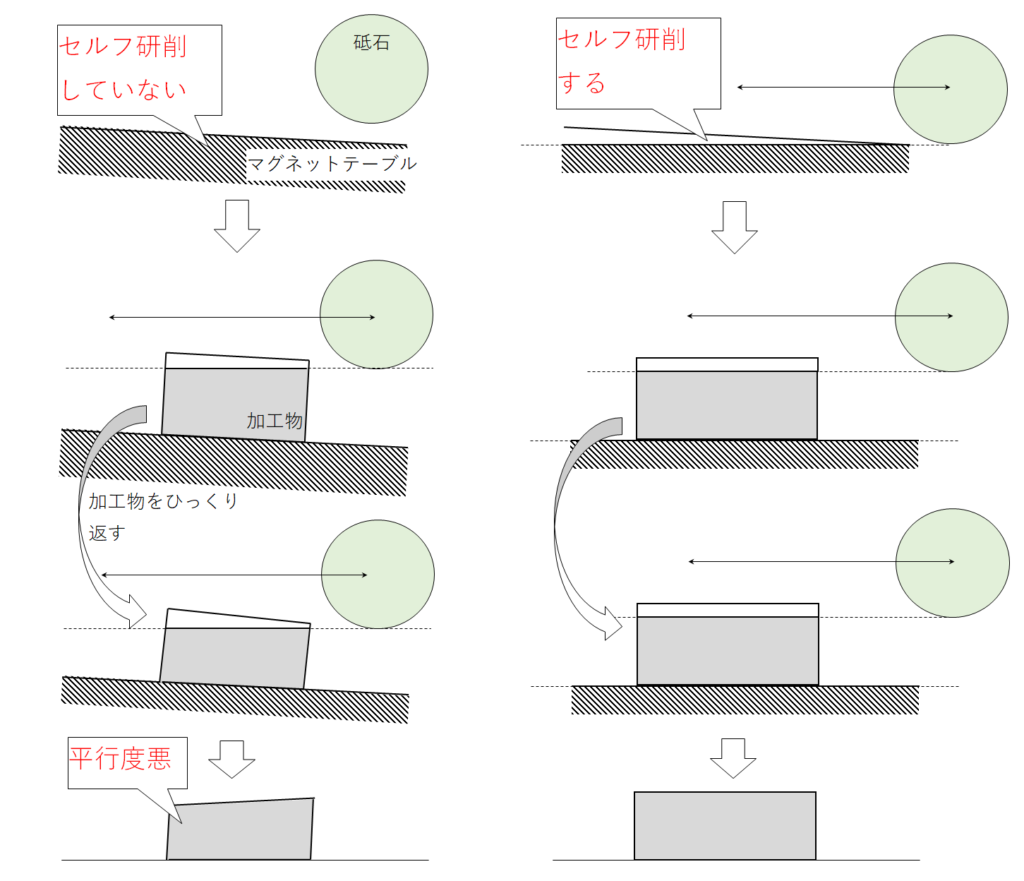
さまざまな研削盤の多くはマグネット(磁石)で加工物を固定することが多いです。セラミックやステンレス(SUS3系)などの非磁性材料を加工するために使用する精密バイスもバイスごとマグネットで固定して使用するぐらいです。このマグネットテーブルはX軸と平行でない状態で加工すると加工面が傾くことになり、加工した両側面が平行にはなりません。そのためマグネットテーブルをX軸の稼働に合せて砥石で加工することでX軸とマグネットテーブルとの並行度の精度を向上させます。このマグネットテーブルを加工機に設置されている砥石で加工することをセルフ研削、ベット研磨ともいいますが、ここではセルフ研削としておきます。
このマグネットテーブルをセルフ研削する場合、注意しなければならない事が大きく2点あります。
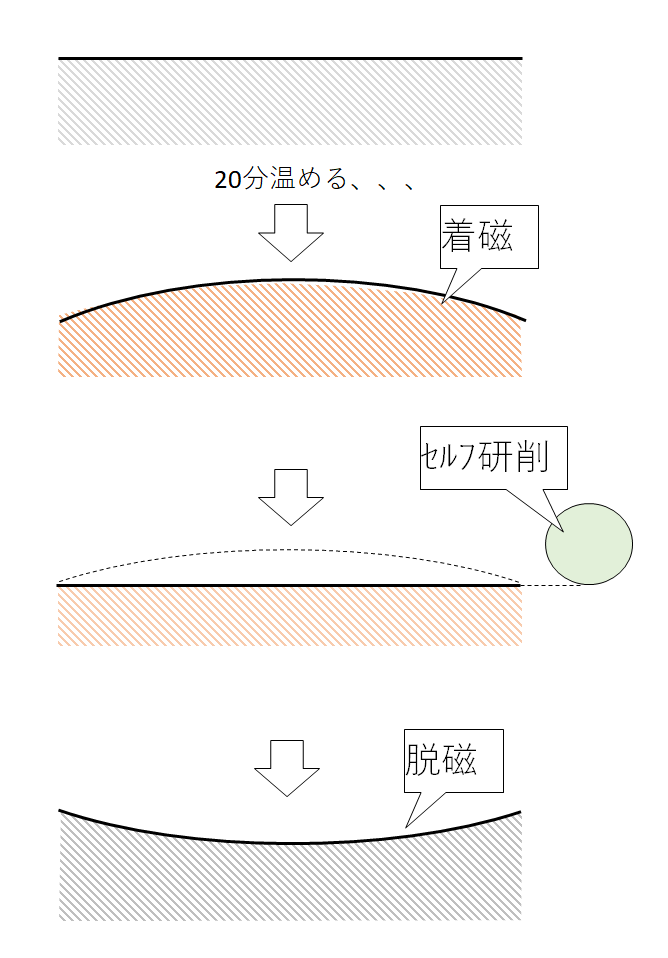
まず1点目はマグネットテーブルは着磁させた状態で加工するということです。マグネットテーブルはクランプ(固定)、アンクランプをするために着磁スイッチのON,OFFをします。着磁させるとテーブル温度が人肌程度に高くなるため、着磁させる前と後ではテーブルの平面度が変わります。当然加工は着磁させた状態で行われるため、着磁させた状態がX軸と平行でなければならりません。そのためテーブルを着磁させた状態を20分程度放置し、テーブル温度が安定するのを待ってからセルフ研削を始めます。
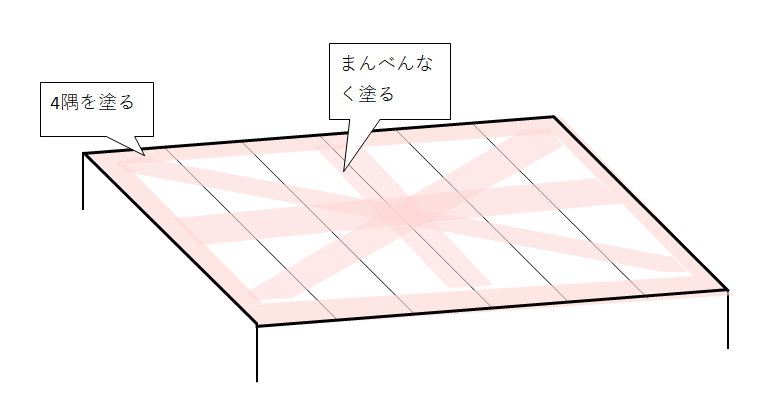
2点目として「テーブル全域を加工しなければならない」です。まず基準となるテーブルに凹凸があると加工精度が悪くなる原因になるためセルフ研削する範囲はテーブル全域が削られていなければなりません。もしテーブルに削り残しがあるとその部分が凹み、加工物が傾いて固定されることが考えられます。テーブルの削り残しがないように加工するテーブル全域をマジックで広範囲で色塗り、着色したすべての箇所が研削加工により除去できれば全域を加工できたことになります。マジックによる着色は特に削り残しが発生しやすいテーブル角部や中央部がまんべんなく塗られていれば、全域塗られていなくても問題ありません。
5.加工ストローク
最後の加工準備は加工ストロークの設定です。加工ストロークはX軸とY軸で加工物のサイズに合わせて設定しますが、テーブルストロークとしてのX軸は砥石が加工物から完全に抜け切る位置にしなければなりませんが、Y軸は仕上がり面の出来栄えが若干変わるため、加工物とそれぞれのストローク方向、量に合わせて加工方法の名前があります。基礎知識として覚えましょう。
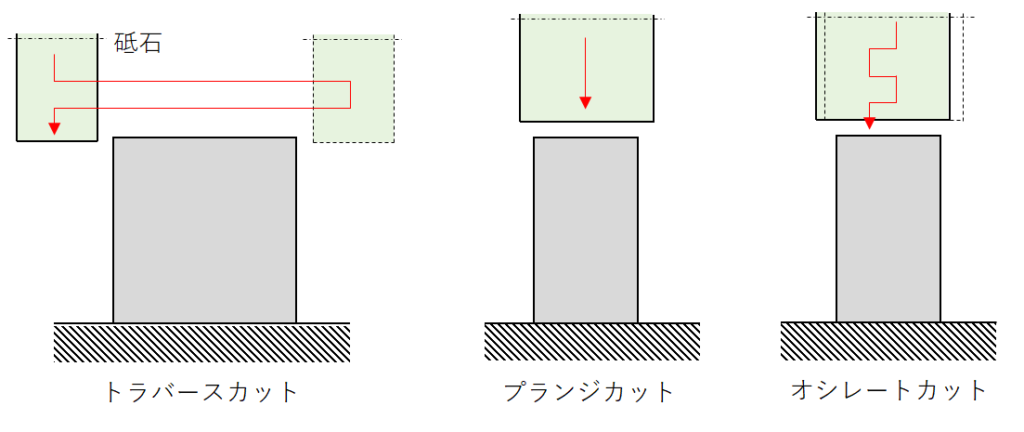
トラバースカット:
加工物から砥石を抜け切るようにストロークする加工、ストローク速度によっては加工物の粗さが変化する。
プランジカット :
加工幅よりも砥石幅が大きくストロークせずにする加工、ドレッシング形状が転写しやすい加工方法でドレス条件で粗さが変化しやすい。
オシレートカット:
加工幅よりも砥石幅が大きいが、わずかにストロークする加工、プランジカットでは粗さが改善しない場合に行うことが多い。
6.加工位置
砥石をセットし、研削液の準備もOK、マグネットテーブルの平行度も問題なく、テーブルストローク量の設定も完了し、これでようやく加工ができます。ですが、どこまでZ軸を下げれば良いかわからないのでこの設定は加工しながらでなければ決められません。砥石の移動領域は大きく「早送り」「エアーカット」「粗加工」「仕上加工」に分類され、それぞれの開始終了点を設定しなければなりません。
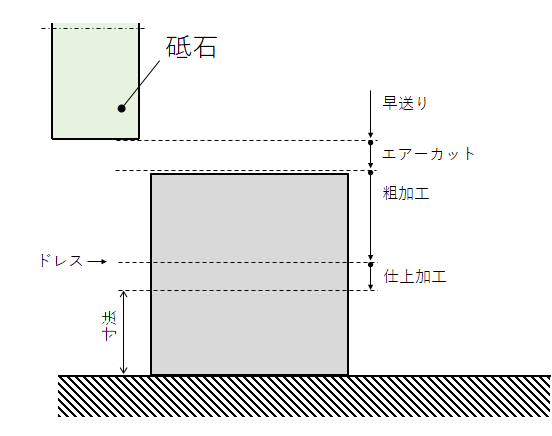
早送り :
Z軸が加工開始位置まで高速で移動する領域であり、加工物と砥石が絶対に接触しない位置に設定しなければならない。
エアーカット:
加工開始位置から砥石と加工物が接触しないだろうと想定される領域、仮に接触しても低速のため加工物への損傷は小さい
粗加工 :
砥石と加工物が接触し、粗加工を行う領域。
仕上加工 :
面粗さを向上させるために仕上加工前にドレスを行い、その後にZ軸を低速送りをする領域。
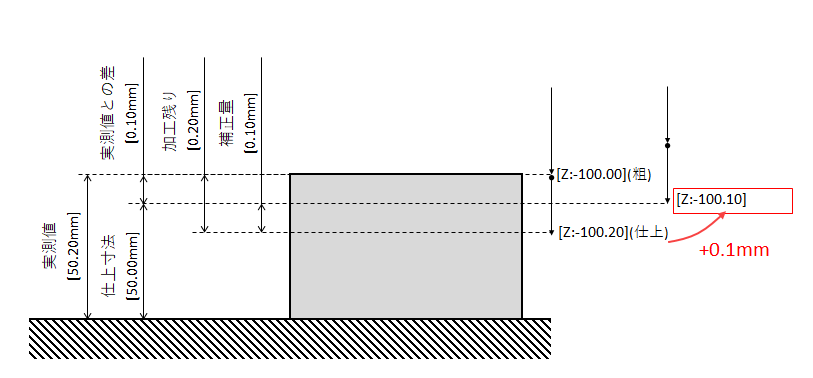
最終的なZ軸の終了点は仕上加工完了点ですが、この位置に達してから加工物の寸法を測定すると削りすぎて、寸法マイナスしていることがあり得ます。そのため粗加工を終えた位置で、一度、加工物の寸法を測定します。この時、加工物の寸法を測定し、実測値とZ軸の座標の加工残りを比べ、その差分を補正値としてZ軸仕上位置を変更することで、加工座標を確定させることができます。
どうでしたか?少しは研削加工を理解できたのではないでしょうか?今回、ドレスについては内容が長くなりそうでしたので次回、詳しく説明したいと考えています。ページの最下部にコメント欄を追加しました。要望やわからない点、感想、苦情‥ など、なんでもよいので書いてもらえると励みになります。ぜひ、お願いします。
以上です。
コメント