1.延性破壊
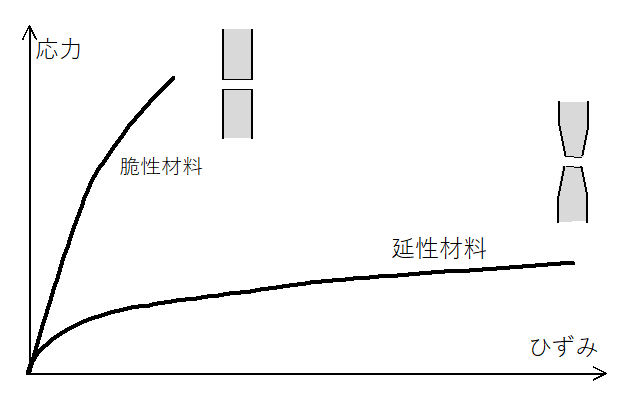
延性破壊とは主に金属材料で発生し、金属材料が固有にもつ降伏応力以上の応力が加わったとき、連続的な塑性変形を伴って、破壊に至る現象とされています。もう少しかみ砕いて説明すると、それぞれの材料には予め弾性変形する限界の応力がありますが、その限界応力を超えるとすぐに破損するわけでななく引き伸ばされつつも、徐々に塑性変形が始まり、破壊までの兆候として亀裂が生じ、破損に至ります。
金属材料には介在物と呼ばれる構成元素とは異なる元素が微量に含まれています。例を挙げると炭素鋼はFe(鉄) C(炭素)以外にも Cu(銅) P(硫黄) Mn(マンガン)などが含まれ、それぞれの元素の延性度合いは異なります。そのため延性破壊は引っ張ると金属材料に含まれる介在物を除いて伸び、介在物周りは空孔ができることで、破断面はカップアンドコーン型となり、拡大するとディンプルと呼ばれる微小な凹凸が見られるのが特徴です。
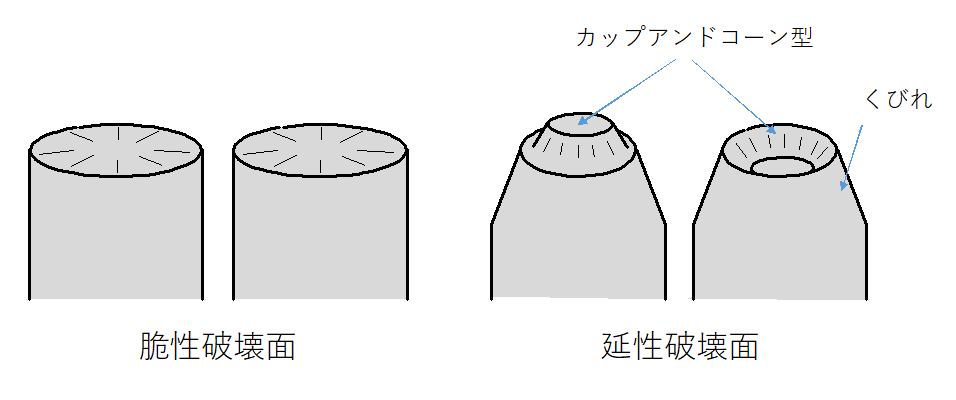
また材料それぞれの弾性変形する延性度合いは炭素鋼、銅、アルミ…などの引張、曲げ試験のデータによってわかりますが、この延性破壊は環境温度が低くなるほど、延性が失われ破損に至る応力が小さくなります。この延性が失われ、脆性をしめすような破壊形態を示すような温度を遷移(せんい)温度と言います。そのため延性破壊の範囲内で設計する場合は、材料選定以外にも使用環境温度にも配慮が必要なんですね。
なお、プレスの打ち抜きなどのせん断加工は延性破壊によって行われる加工なので、打ち抜き面を見ると見た目でせん断面(弾性)と破断面(塑性)の違いがわかります。
2.脆性破壊
弾性変形よりも塑性変形が主で破損に至る現象を脆性(ぜいせい)破壊と呼びます。この脆性破壊は素材として延性が低いガラス、陶器以外の材料である水素を吸収した鉄鋼、鋳鉄などでも生じます。前述したように延性破壊は環境温度に依存するため、低温環境でも脆性破壊に至り、これを低温脆性破壊と呼びます。さらに延性が高い材料であっても部品形状の差によって、応力が高まり易く、即座に弾性変形領域を超え、脆性破壊に至る切り欠き脆性破壊という現象(後述する応力集中による破損)もあります。なお、同じ延性が高い材料でも金属材料に含まれる粒界の不純物(介在物の量、大きさに偏りがあると)によっても、想定外な脆性破壊に至ることもあり得ます。脆性破壊は延性破壊と違い、伸び、亀裂などの破損の兆候が見られないことから、機械を設計する上で避けたい現象です。そのため機械部品設計をする上で、使用環境温度、切り欠きなどの形状を留意してシャルピー衝撃試験の結果も踏まえ、材料選定をすべきです。
衝撃試験に関する記事はこちらを参照
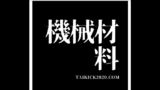
3.疲労破壊
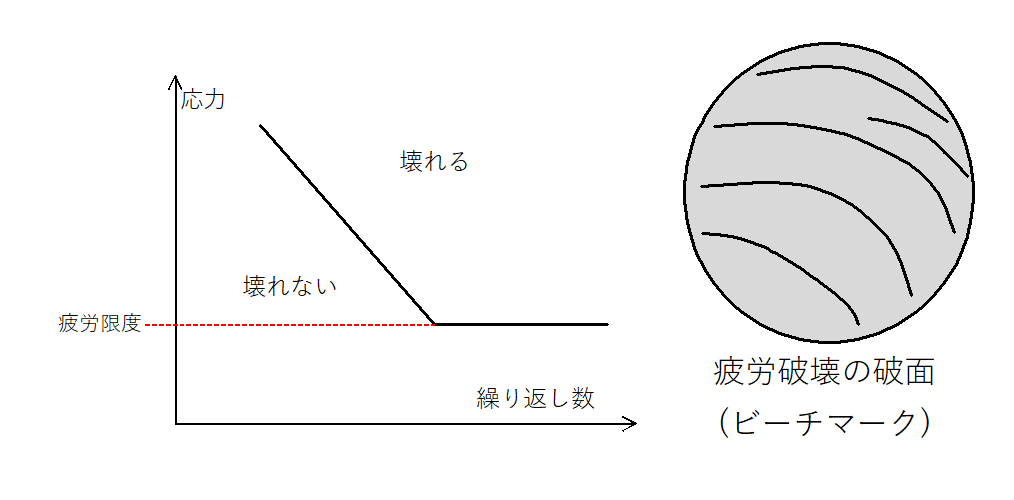
前述した例外的な(低温、切り欠け)脆性破壊を除き、金属材料は弾性領域を超える負荷で破壊しますが、低負荷でも何度でも繰り返し負荷をあたえ続けると破壊に至ります。通常、弾性変形により応力、ひずみは元に戻りますが、ミクロ構造は元に戻らないため、弾性変形をせずに脆性破壊のように破損する現象を疲労破壊と言います。また疲労破壊は応力が大きい程、少ない回数で破壊し、応力が小さい程、多い回数で破損しますが、ある一定以下の小さな応力では疲労破壊はしません。これを疲労限度と定義されています。炭素鋼には疲労限度が定義されていますが、非鉄(アルミ、銅)はデータの再現性が低く、データが収束しないため、明確にはされていません。なお、疲労破壊した場合、その破面を観察すると貝殻のように小さな破面が何層にも重なったようなビーチマークと呼ばれるものが確認できるため、金属が伸びずに脆性破壊した時、破断面を見れば、疲労か?脆性か?の違いは判別できると思います。
4.応力腐食割れ
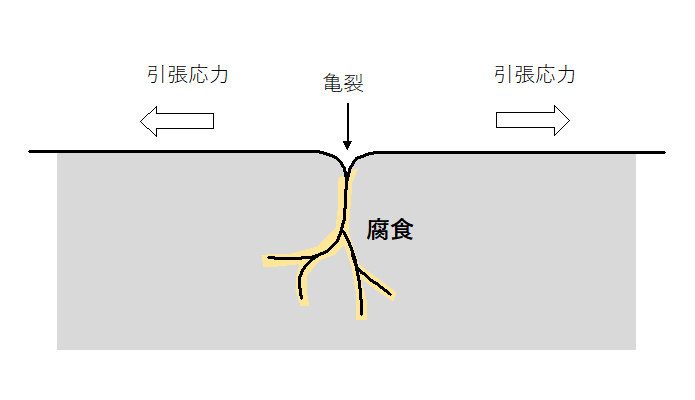
塩水、酸などの腐食環境下で応力が加わったとき、小さな静荷重でも脆性破壊する現象が応力腐食割れです。この応力腐食割れは以下の3つの要素が合わさる時だけに生じる特徴があります。
・引張応力にて発生するため、圧縮応力では発生しない ・純金属では発生せず、合金のみでしか発生しない ・塩水、酸が含まれるような状況下での使用で発生する
この破損は上記3つの要素をひとつでも排除すれば、予防することができるため、真鍮、青銅、などの銅合金から純銅に材質を変更することで対策できます。また一定の引張応力に耐えうるように表面に圧縮応力をショットピーニングで与える処理でも有効になります。さらに加工、溶接などの熱により組織が変態したり、冷却時の引張残留応力が残るため焼鈍を行い、応力除去をすることも予防のひとつとして挙げられます。錆予防としてステンレスを選定することが多いですが、キッチン周りで使用されるような、一般的に多く流通しているオーステナイト系ステンレス(SUS304)は発生しやすく、航空機、船舶などに使用されるフェライト径ステンレス(SUS329J1)は発生しにくい特徴があります。なお、応力腐食割れは破損に至るまでに腐食による微細な亀裂が徐々に発生するため、非破壊検査などで定期的に早期発見することができます。
非破壊検査はこの記事を参照
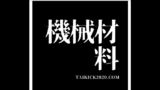
5.クリープ破壊
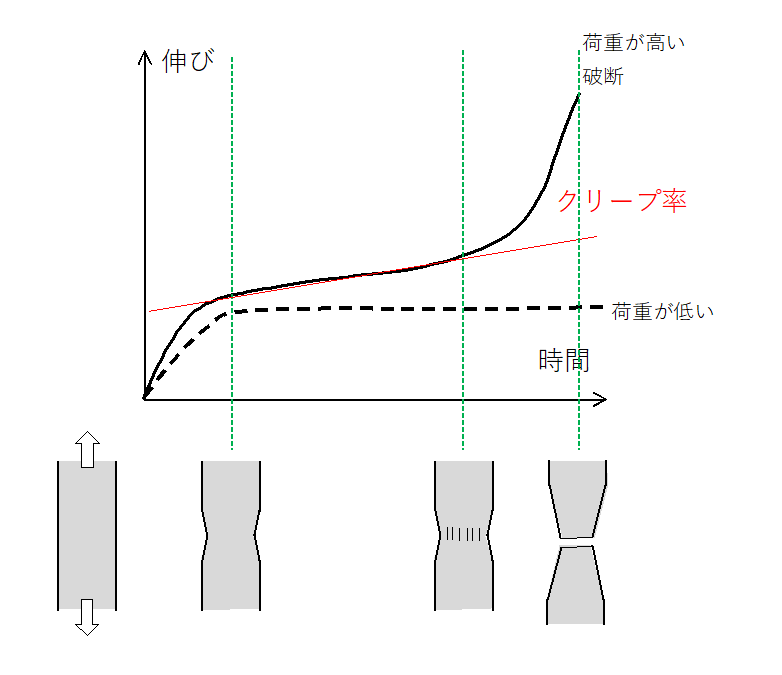
材料に一定荷重を加えてひずみを生じさせた時、そのひずみが時間と共に進行し、後に破損に至る現象をクリープ破壊と言います。クリープは結晶粒界面に生じる空気のすきま(ボイド)が時間経過とともに小さな亀裂を生み、やがて大きなひずみ、破壊に至ります。このクリープは高温、高荷重であればある程、起こりやすく、樹脂は金属よりも低い温度で起こりやすい特徴があります。クリープは三段階の変形を経て起こります。第一段階では急速に変形が発生し、時間経過と共に徐々に変形する第二段階を経て、第三段階で急激な変形により破損します。荷重が低かったり、環境温度が高くない場合は第一段階だけの変形になるため、この第一段階だけの変形に留まる最大応力を「クリープ限度」といいます。特にねじは構造上一定期間、応力をあたえ続けるために、高温下での使用を検討する際はこのクリープ限度を知るために高温下で試験を行い、クリープ限度を調べる必要があります。なお近年、クリープ破壊を防止するために耐熱鋼(SUH)以外にも樹脂、ゴムの耐クリープ材料も開発されています。
6.摩耗
上述したものはすべて破壊であり、部品がちぎれたり、破れたりする現象ですが、ぱっと見の変化はないことで、損傷状況が判断しにくいものが摩耗です。摩耗は以下のようなにいろいろな形態がありますが、金属材料で生じる摩耗のほとんどは凝着摩耗を疑います。

凝着摩耗: 接触する二面間にすべりが生じる事でどちらかの軟らかい材料の方が粒子状に脱落する(摩耗粉) アブレッシブ摩耗: 二面の内の一方の表面にある凸がもう一方に食い込んだ状態で摩耗する。すべり面に異物が混入した場合も同様に摩耗する。
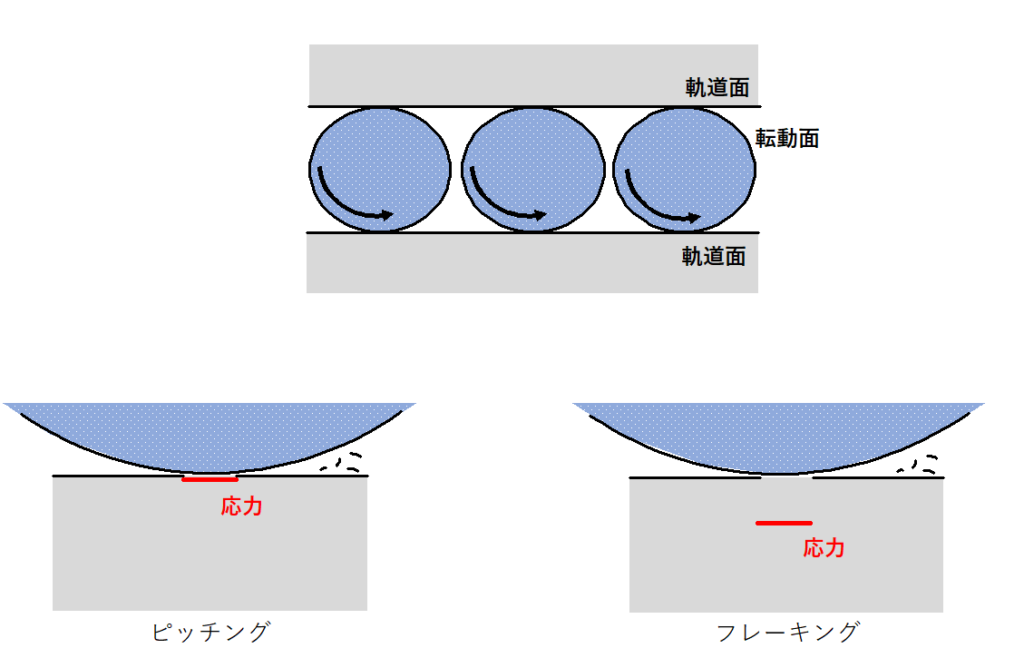
疲労摩耗:小さい負荷でも繰り返し負荷を受け続ける事ですべり面がはくり損傷する摩耗 〇ピッチング:材料表面にはくりが生じる 〇フレーキング:材料内部が起点となってはくりが生じる
他にも個体、液体、気相の衝突による物理的な損傷によるエロージョン摩耗、薬品などによる科学的な浸食現象による腐食摩耗が挙げられます。
凝着摩耗、アブレッシブ摩耗、エロージョン摩耗は材料表面が硬い程摩耗しにくく進行し難いため、硬度上昇が必要ですが、アブレッシブ摩耗では片面だけを軟らかくすることで食いつきによる摩耗の進行が改善します。基本的に同じ材質同士の材料は凝着摩耗が進行しやすいため、潤滑油や表面粗さを改善することが有効とされています。
7.フレッチング
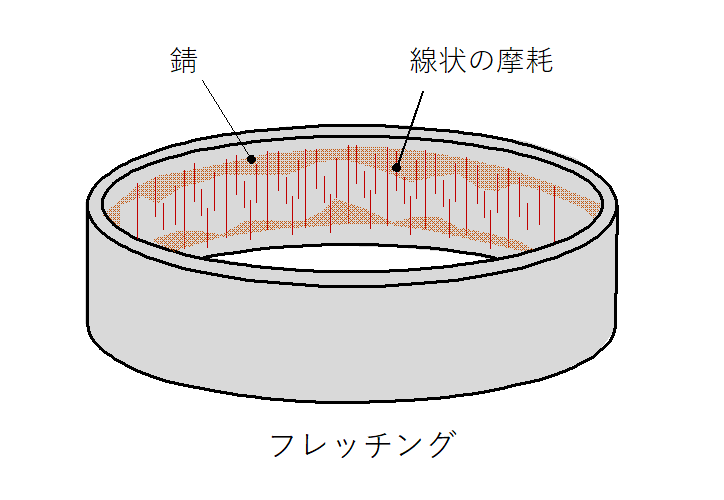
主に軸受などのはめあい面に見られる摩耗で、赤黒色の線状の摩耗が低ピッチで発生する現象です。発生のメカニズムとしては接する二面間に微小なすべり接触が継続的に続くと、その部分に摩耗、腐食、疲労の複合的な微小な損傷が起こります。フレッチングは軸とハウジングの間のはめあい面のすきまが大きかったり、機械の運動パターンが振り子運動のような揺動運動であると同じ箇所に繰り返しすべり接触が生じ発生しやすくなります。また機械の動作が早かったり、高タクト運転であると機械そのものの振動が大きく意図しない箇所でフレッチングが発生することもあります。動作パターンの見直しや、はめあい面に油を塗布することで改善策します。またはめあい面のすきまを小さくすることで位置エネルギーを小さくすることで発生を防ぐことができ、さらにはめあいをしまりにしたり、軸受を予圧にすることで大きく改善できます。
8.応力集中
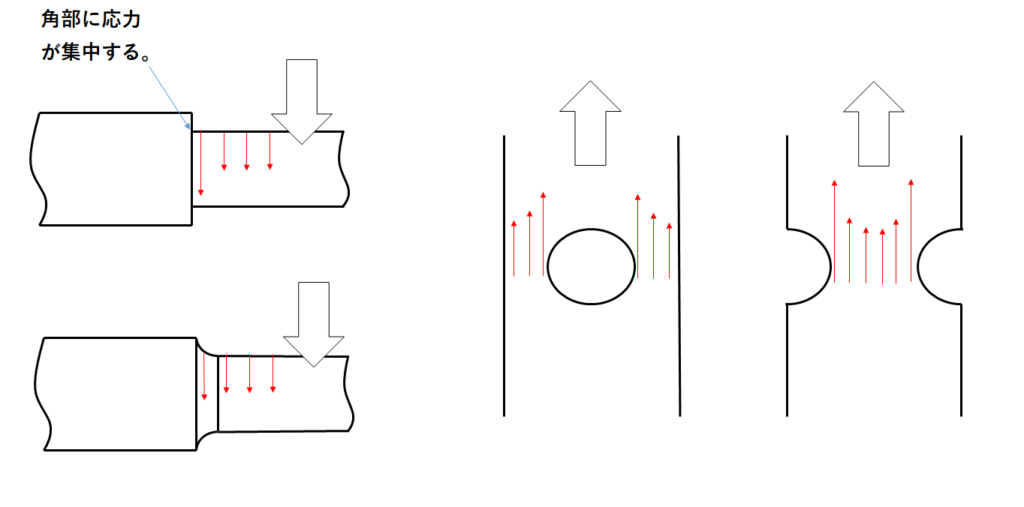
どのような材料でも負荷が加わると応力が発生し、断面形状が一様であると応力分布も一様になります。しかし厚い部分、薄い部分があったりと断面形状が一様でないと、応力分布にも偏りが生じます。この応力分布の偏りにより局所的に応力が集中する箇所が発生します。この応力集中により破損に至る現象を応力集中破壊と言います。この応力集中による破壊を防ぐためにはFEM解析などを使用して設計時に機械部品に加わる荷重がどのように応力分布するかをシュミレーションすることが大事です。また構造的に応力が集中しやすい部分は以下のようにピン角ではなく、R角にすることでも未然に防ぐことができます。何気なく設定している隅R寸法などはRの大きさによっては破損に至るケースも良くあるんですね。
9.まとめ
・弾性変形しながら、徐々に塑性変形し破損に至る現象を延性破壊、弾性変形を伴わず、塑性変形が主で破損に至る現象を脆性破壊と言う
・最大応力以下の負荷であっても、繰り返し負荷を受け続けると破損する現象を疲労破壊と言う。
・腐食によって、小さな応力でも脆性破壊する現象を応力腐食割れと言う。
・一定時間、負荷をあたえ続けると破損する現象をクリープ破壊と言い、高温下であるほど小さな負荷で発生しやすい。
・摩耗には「凝着摩耗」「アブレッシブ摩耗」「疲労摩耗」があり、摩耗対策はどの摩耗であるかを特定することが重要。
・フレッチングははめあい面で生じ、振動や繰り返し運用で進行する破損形態である。
・一定負荷であっても形状によって応力分布は一様ではないため、応力が集中し破損に至るケースがある。
以上です。
コメント